Busan's Manufacturing Revival Through Digital Innovation
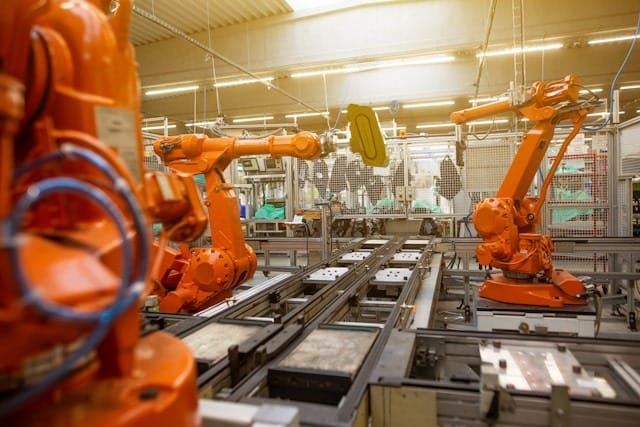
Busan, South Korea — A city built on the strength of its manufacturing prowess now faces an industrial reckoning. Once a titan of shipbuilding and heavy machinery, Busan’s manufacturing sector now struggles against the tide of global innovation and an aging industrial base. Yet, amidst these challenges lies an opportunity for transformation—one powered by the tools of the Fourth Industrial Revolution.
With the rise of digital technologies such as the Internet of Things (IoT), artificial intelligence (AI), and robotics, Busan has the chance to breathe new life into its industries and reaffirm its place as a leader in manufacturing. But the question remains: can Busan embrace change fast enough to secure its future?
For decades, Busan's factories were symbols of South Korea's rapid industrial ascent. Industries like shipbuilding and automotive manufacturing once drove the city's economy, securing jobs and fostering growth. Today, however, the cracks in this foundation are apparent. Rising operational costs, outdated equipment, and declining productivity paint a grim picture.
Economic data reveals that Busan’s manufacturing output has plateaued, contributing to a shrinking share of regional GDP. Small-to-medium enterprises (SMEs), which form the bulk of Busan’s industrial sector, find themselves particularly vulnerable. “We are working harder than ever, but the margins are thinner, and the future feels uncertain,” remarks one factory manager in the city's machinery sector.
The world is moving toward a new era of "smart manufacturing," where technology is king. For Busan, the integration of digital solutions like IoT sensors, AI-driven analytics, and automated robotics could be transformative. These tools not only improve efficiency but also unlock new potential by optimizing workflows, predicting maintenance needs, and responding dynamically to market shifts.
For example, smart factories equipped with real-time monitoring systems have demonstrated up to 30% reductions in downtime and significant cost savings globally. Applying these technologies across Busan’s industries could yield similar benefits. “Smart manufacturing isn’t just the next step—it’s the survival kit for modern industry,” emphasizes a policy analyst at the Busan Chamber of Commerce.
Recognizing the urgent need for transformation, both national and local governments have rolled out initiatives to bolster digital adoption. The South Korean government’s "Smart Factory Initiative" aims to install advanced systems in 30,000 manufacturing facilities nationwide by 2022. These systems leverage IoT and AI to create more responsive, efficient production environments.
Locally, Busan has outlined its "Digital Economy Innovation Strategy 2030," a roadmap designed to transform the city into a hub for advanced manufacturing. Central to this vision is the Busan Smart Manufacturing Innovation Center, a collaborative space where SMEs can access technology, training, and funding support.
Despite robust policy backing, the path to digital transformation is far from smooth. Many SMEs struggle to afford the initial costs of digital upgrades, including new equipment and staff training. Cultural resistance also plays a role, as some manufacturers remain hesitant to disrupt traditional workflows.
Another key challenge is the skills gap. “You can’t just install new machines and expect miracles,” explains a technology consultant working with Busan SMEs. “Workers need to understand how to use them effectively.” Without targeted retraining programs, the benefits of digitalization may remain out of reach for many.
The promise of digital transformation extends beyond improved efficiency. Busan has the potential to redefine its industrial identity by venturing into high-value sectors such as marine technology, green manufacturing, and advanced materials. The rise of South Korea’s Green New Deal further incentivizes manufacturers to adopt eco-friendly practices, integrating sustainability into their operations.
Take the case of a local parts manufacturer that implemented IoT sensors to track energy use across its factory. The company reported a 20% reduction in electricity costs within six months—a clear demonstration of how digital tools can support both economic and environmental goals.
Busan is not alone in its struggle to modernize. Cities like Munich and Singapore have successfully transitioned to high-tech manufacturing by fostering strong public-private partnerships and prioritizing innovation. Singapore’s "Smart Nation" initiative, for example, integrates advanced technology into nearly every aspect of its economy, from industry to urban planning.
Busan can draw inspiration from these models, emphasizing collaboration between government, academia, and industry to build a sustainable ecosystem for digital manufacturing.
The road ahead is neither simple nor without risks. Yet, with determination and coordinated efforts, Busan can overcome the hurdles of digital transformation. The city’s government, businesses, and workers must come together, aligning their goals to ensure that technology is not seen as a threat but as a tool for growth.
Busan stands at a crossroads. Its choices today will shape the destiny of its manufacturing sector—and perhaps its entire economy—for generations to come. By embracing innovation, fostering collaboration, and investing in its people, Busan can chart a path toward a brighter, more sustainable industrial future.
Comments ()